En este artículo evaluaremos las acciones a tener en cuenta para maximizar la fiabilidad de las instalaciones, consiguiendo de esta manera una alta disponibilidad y reduciendo las intervenciones correctivas.
Podemos dividir las acciones a tener en cuenta en dos grupos:
- Antes de la puesta en marcha de la instalación.
- Durante la operación de la planta.
Acciones a realizar antes de la puesta en marcha de la instalación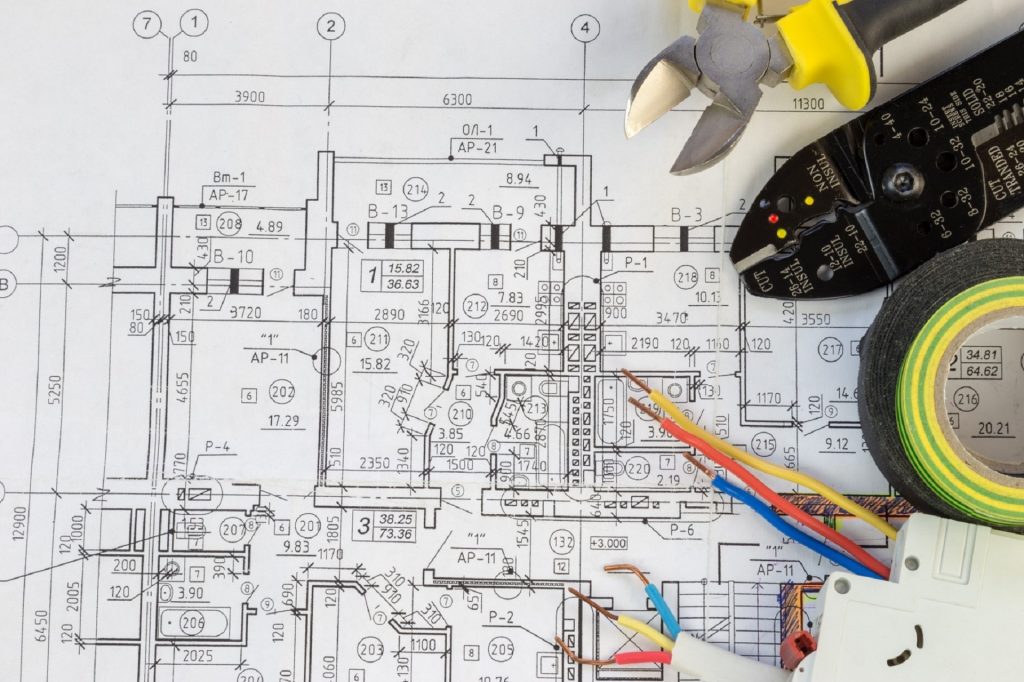
Para maximizar la fiabilidad de las instalaciones, es necesario contemplarla desde el diseño como una de las tres patas del estudio RAM (Reliability, Availability and Maintainability). Este estudio debe realizarse antes de la construcción de cualquier planta, centro de producción, etc. La fiabilidad, disponibilidad y mantenibilidad son factores que están relacionados y han de analizarse en conjunto para conseguir el funcionamiento óptimo de la instalación.
Para que el análisis RAM sea efectivo, hay que tener en cuenta una serie de factores:
Expectativas de producción y disponibilidad de la planta.
Es imprescindible calcular estos valores para las fases de puesta en marcha y operación. Los cálculos han de tener en cuenta la vida útil de los activos para, de esta forma, estimar el tiempo que el centro estará operativo y planificar medidas para alargar su producción.
Clasificación de los activos según su criticidad dentro de la instalación.
En base a las expectativas de producción y disponibilidad, se dimensiona la instalación de forma que los activos más sensibles o críticos sean redundantes, puedan pararse para su mantenimiento sin afectar a la operación de la planta, y no ocasionen bajadas de producción si se averían.
Estrategias de mantenimiento.
Es muy importante que se tengan en cuenta las distintas estrategias de mantenimiento a realizar sobre los activos y la facilidad de realizarlos. De esta manera conseguiremos que los activos más críticos y aquellos que tienen mucho mantenimiento preventivo estén correctamente ubicados, facilitando a los técnicos realizar sus labores en el menor tiempo posible y con la máxima seguridad. No será tan importante la ubicación de activos poco importantes que no afecten a la producción o que tengan poco mantenimiento planificado.
Documentación de la instalación y formación del personal
Una vez que hemos decidido los activos a instalar y su ubicación, es necesario documentar la función que realiza cada uno de ellos, y como afectaría al resto una avería que no le permitiera operar correctamente. Este análisis nos permite detectar cuellos de botella que reducirían sensiblemente la fiabilidad.
Por último, es necesario que todo el personal de operación y mantenimiento esté formado en el funcionamiento de la planta, de los activos más sensibles, y que sea consciente de las consecuencias de las averías principales que pueden producirse en el centro.
Acciones a realizar durante la operación de la planta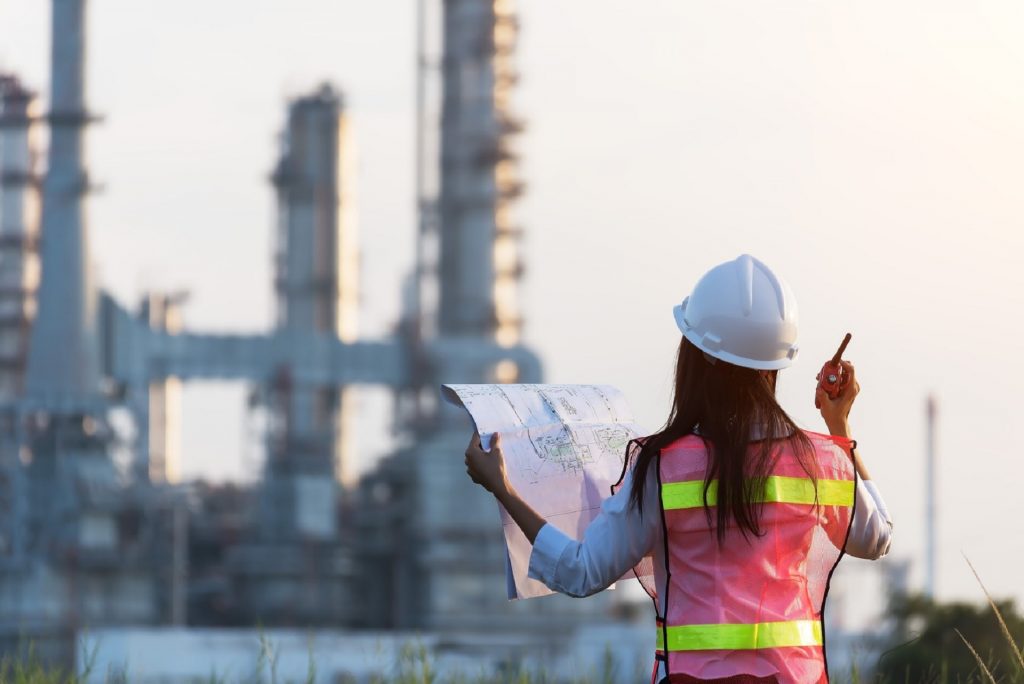
Una vez que un centro está en marcha, su fiabilidad estará limitada por las características de su diseño. La modificación de la instalación una vez en marcha es mucho más costosa y puede suponer la parada de producción para implementar los cambios necesarios para aumentarla.
Por tanto, únicamente se realizan las modificaciones de diseño que solventen problemas graves de productividad o que generen un coste de mantenimiento tal que anule el beneficio.
En consecuencia, en la mayoría de los casos las tareas están enfocadas a mantener el nivel de fiabilidad del diseño:
Revisión del correcto funcionamiento de los activos.
Trabajos que tienen como objetivo comprobar que los activos funcionan correctamente de acuerdo con lo previsto en su diseño. Es decir, que funcionan correctamente y dentro de los rangos operativos definidos.
Optimizar las gamas de mantenimiento. Respetar todos los mantenimientos preventivos definidos en el diseño y monitorizar constantemente los mantenimientos predictivos. El objetivo es evitar la generación de averías que reduzcan la fiabilidad de la planta. Podemos utilizar la aproximación del Mantenimiento Productivo Total (TPM) para conseguir optimizarlo e involucrar a todo el personal del centro en el mantenimiento.
Asegurar la correcta operación de los activos. Es imprescindible que los operarios conozcan los activos que operan o que gestionan. Esto se consigue formando al personal no solo en operación, sino en la realización de tareas de mantenimiento básicas como engrases, inspecciones visuales, toma de mediciones, limpieza, etc (mantenimiento autónomo).
Establecer KPIs de rendimiento. Los KPI Permitirán comprobar que la instalación obtiene la fiabilidad requerida cumpliendo con la producción y el control de costes establecido.
Estudiar mejoras del centro que no paren la productividad o que corrijan problemas de diseño graves. Por ejemplo la instalación de una línea de reserva para corregir un cuello de botella, actualizaciones de hardware / software de equipos para mejorar su funcionalidad, mejoras en la seguridad para los trabajadores, propuestas de operadores o personal de mantenimiento, etc.
Conclusión
Para maximizar la fiabilidad de las instalaciones es necesario implementarla en todas las fases de diseño de la misma. En esta fase es fácil corregir problemas como paradas totales provocadas por un activo más dimensionado, cuellos de botella, situaciones no controladas provocadas por la avería de un activo, etc.
Una vez que el centro está en producción, las actividades se centran en conservar el nivel de fiabilidad del diseño. Es posible realizar cambios de diseño, pero son mucho más caros y normalmente se realizan para corregir problemas graves de control de costes o productividad.
¿Necesitas más información?- Contacta con nosotros