En esta entrada definimos de forma resumida qué es el mantenimiento productivo total y sus principales características. TPM (Total Productive Maintenance) es una aproximación al mantenimiento de equipos que se enfoca en alcanzar la producción casi perfecta: sin averías, paradas imprevistas, enlentecimiento de la producción, defectos ni accidentes. El TPM enfatiza un Mantenimiento proactivo y preventivo para maximizar el ciclo de vida y productividad de un equipo.
EL Mantenimiento Productivo Total se integra dentro de la Gestión Total de la Calidad, Total Quality Management o TQM. Mientras que la TQM está basada en la calidad en su conjunto y de todas las operaciones, el TPM se centra en los equipos y las líneas de producción. Ambas son filosofías que trabajan en un tándem para entregar productos o servicios de calidad a los clientes.
¿Cuál es el objetivo del TPM?
La mayor diferencia entre el TPM y otras filosofías de Mantenimiento es que todos los integrantes de la empresa se involucran en el proceso. El concepto de “Yo operario de producción, produzco y el responsable del mantenimiento, arregla “ o “Yo lo arreglo cuando deja de funcionar” no se sigue y se cambia por “Yo operario de producción me responsabilizo de los equipos y herramientas con los que trabajo” “Yo del departamento de Mantenimiento tengo que prevenir antes de que deje de funcionar” Tanto operarios, técnicos como gestores forman parte del TPM.
El objetivo del TPM es optimizar al máximo la productividad, para llegar a los cinco ceros:
“Cero averías, cero defectos, cero despilfarros, cero accidentes y cero contaminaciones”
A través del TPM, se promueve que tanto operarios como gestores sigan rutinas establecidas alrededor de inspecciones diarias, limpiezas o lubricaciones de máquinas y con ello se puedan observar potenciales problemas antes de su aparición. Por tanto, con el TPM se intenta:
- La aproximación a un ciclo de vida de las máquinas que mejoren el funcionamiento de toda la línea de producción hacia el casi perfecto.
- La mejora de la productividad a través de empleados motivados y cualificados.
- Involucrar a todo el personal de la empresa.
- Que el uso de actividades cotidianas formen parte de la rutina diaria a través de las cuales se pueden identificar posibles fallos.
¿Cuáles son los pilares del TPM?
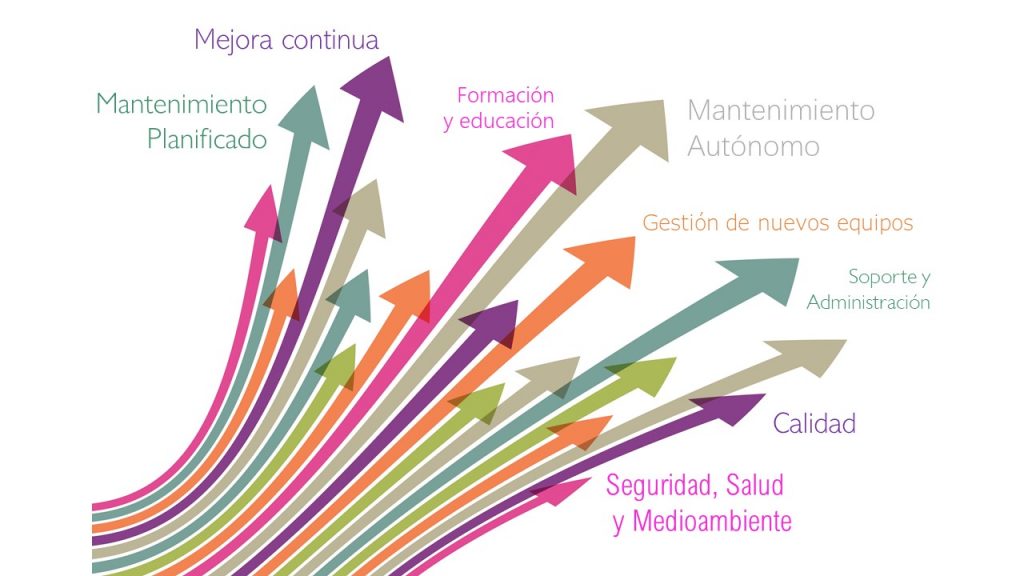
Mantenimiento Autónomo: los operarios monitorizan las condiciones de las areas de trabajo y de los equipos con los que trabajan. En nuestro blog encontrarás un artículo sobre ello aquí.
Mejora Continua: la clave es tanto elegir los problemas correctos como asegurar que éstos se resuelven. Se pretende llegar a la raíz del problema para definirlo y calcular el tiempo necesario para solventarlo. Asimismo, conserva y transmite la experiencia adquirida en la reparación para aplicarla en el futuro. El objetivo es reducir las 6 grandes pérdidas, que son debidas a:
- Averías
- Ajustes y configuración
- Tiempos muertos y paradas menores
- Defectos de calidad en el trabajo hecho
- Reducción de velocidad
- Arranque inicial
Mantenimiento Planificado: se sistematiza un método de actividades para alcanzar un estado óptimo de las máquinas y una mejora continua de los procesos.
Calidad: cuando la responsabilidad de las condiciones de operación y de mantenimiento son compartidas entre todo el personal, se promueven ideas y acciones de mejora de calidad desde todas las áreas de trabajo.
Gestión temprana de los equipos nuevos: desde el inicio, los coordinadores de equipos planifican el mantenimiento de los nuevos equipos durante todo su ciclo de vida e informan a los gestores de los resultados.
Formación y educación: la formación y educación continua de los empleados, no sólo es parte de la mejora continua, también aumenta su motivación y eficiencia y promueve la retención de personal capacitado y con experiencia.
Soporte y Administración: tanto el personal de soporte a la producción, como personal administrativo y los mandos están involucrados en el proceso del TPM, lo que se traduce en mejorar todos los procesos con el objeto de minimizar pérdidas o desfases y compartir la información que se obtiene de la aplicación del TPM.
Seguridad, Salud y Medioambiente: son aspectos básicos para una política TPM. No existe una unificación a la hora de aplicar medidas concretas, excepto el establecimiento de las mismas como prioritarias.
Un ejemplo de tareas a realizar siguiendo el TPM
Diariamente por el operario de producción:
- Comprobar los puntos críticos de las máquinas con la que trabaja: pérdidas, cambios de presión, niveles de aceite, etc.
- Anotar desviaciones y notificarlas si implican un riesgo.
Estas tareas diarias no deberían llevar más de 10 minutos.
Semanalmente por los miembros del equipo de trabajo:
- Evaluación de los hechos de mantenimiento más importantes.
No debería emplearse más de 1 hora semanal.
Mensualmente por el equipo de Mantenimiento:
- Planificación mensual del mantenimiento a realizar
- Evaluación de las causas, equipos, condiciones de seguridad, etc.
Anualmente por el equipo de Mantenimiento:
- Tareas mayores de mantenimiento planificado
- Evaluación continua y mejora.
Las cuatro fases TPM hacia el objetivo “Fallo Cero”
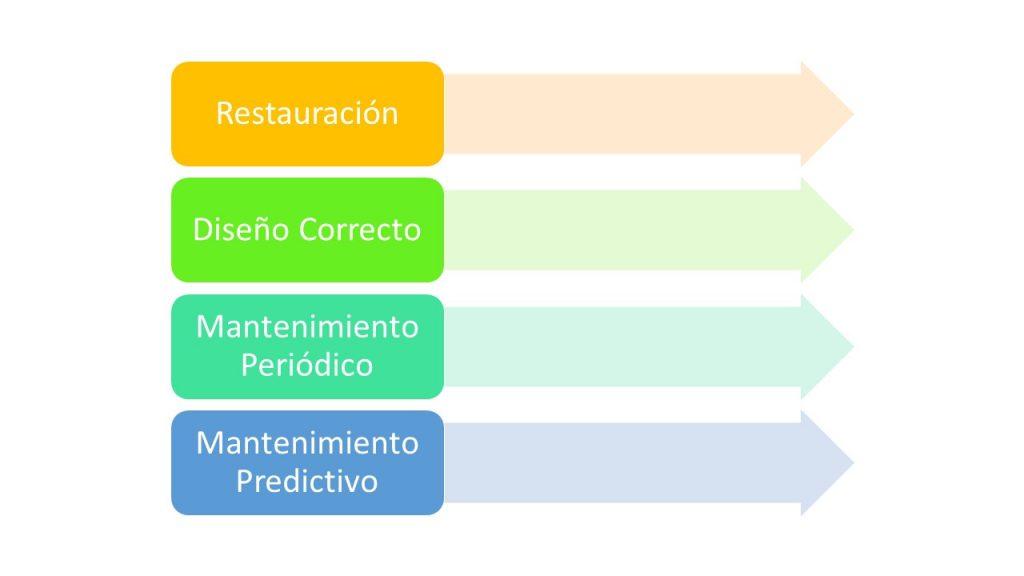
La filosofía TPM plantea distintos estadios hacia el Fallo Cero. Estas fases ayudan a definir objetivos y tareas.
Fase 1: Restauración. En esta fase inicial el objetivo es rectificar el deterioro previo de un equipo que no ha sido reparado, eliminando un potencial deterioro mayor. Con ello, se espera reducir los intervalos de fallo.
Fase 2: Diseño Correcto. En la fase dos, se rectifica el aspecto externo de deterioro, se eliminan los fallos esporádicos y se mejoran los defectos de diseño. El objetivo es alargar el ciclo de vida del equipo lo máximo posible.
Fase 3: Mantenimiento Periódico. Cuando se ha conseguido estabilizar la producción del equipo, se pasa a de forma periódica realizarle mantenimiento, intentando captar cualquier síntoma de funcionamiento anormal del equipo. El objetivo de esta fase es corregir regularmente el deterioro de la máquina.
Fase 4: Mantenimiento Predictivo. La última fase en la que las tareas se centran en la predicción de la producción del equipo basándose en tecnología de diagnóstico y el análisis tecnológico de potenciales fallos. El objetivo es la predicción del ciclo de vida del equipo.
Conclusión
TPM es una filosofía de mantenimiento de la que solo hemos dado una pincelada. El TPM se enfoca en crear un entorno que garantice la entrega de productos o servicios de calidad, sin grandes paradas o sorpresas durante su producción.
Esta filosofía de Mantenimiento puede plasmarse en un Plan de Mantenimiento cuya elaboración es un servicio que ofrecemos en Aeromarine y gestionarse con la ayuda de un software de mantenimiento o GMAO como Amos.
Si tiene cualquier duda o quiere ampliar información, contáctenos.