La mayoría de los departamentos de mantenimiento no están suficientemente dimensionados para cubrir los trabajos a realizar en una instalación. Esto implica el retraso de muchos mantenimientos, la posibilidad de paradas de máquina no programadas, la externalización de parte de los preventivos y, en resumen, la perdida de eficiencia y disponibilidad del centro. Una buena estrategia para corregir estas deficiencias es la utilización de la estrategia de mantenimiento autónomo.
Mantenimiento autónomo: Implicando a todo el personal en los trabajos
El mantenimiento autónomo es parte del Mantenimiento Productivo Total (TPM) que es el proceso en el que se utilizan sistemas, máquinas, componentes, empleados y procesos de apoyo para mantener y mejorar la integridad de la producción y del mantenimiento de una instalación. Su objetivo es evitar las averías y las paradas no planificadas, retrasando el gasto de repuestos y evitando los accidentes.
El mantenimiento autónomo propone que los operadores de las máquinas estén involucrados en parte de los trabajos a realizar. Es decir, cada trabajador inspecciona y monitoriza el equipo en el que trabaja, chequeando parámetros establecidos previamente y avisando a mantenimiento ante cualquier eventualidad que no pueda resolver.
En principio se deben de incluir como mantenimientos autónomos, todas aquellas revisiones que no impliquen un trabajo técnico complejo o el desmontaje de una máquina. Algunos ejemplos podrían ser: las revisiones visuales, las labores de limpieza, toma de datos de parámetros, etc.
¿Cómo podemos aplicar el mantenimiento autónomo?
La aplicación de esta estrategia debe partir desde dirección y cumplir una serie de pasos que garanticen su funcionamiento. En nuestra opinión, lo pasos básicos que se deberían de realizar son:
- Analizar las gamas de mantenimiento de toda la instalación, decidiendo cuales pueden ser realizadas por los operarios.
- Crear acciones formativas específicas, que permitan que cada operario sepa realizar las tareas asignadas, cada cuanto se deben de realizar y en qué condiciones (máquina parada, arranque, calentamiento, enfriamiento…)
- Formar a todos los trabajadores en el funcionamiento y operación de cada máquina, y de su papel en el conjunto de la instalación. Esta formación permitirá que los trabajadores conozcan las consecuencias que tiene en el negocio la parada de un sistema determinado.
- Incentivar las propuestas de mejoras en el mantenimiento por parte de los operadores, que permitirán optimizar constantemente los planes.
- Definir KPIs para comprobar la evolución del trabajo realizado por los operarios, el ahorro en costes que proporciona esta estrategia y el impacto de la misma en la disponibilidad y eficiencia del centro de trabajo.
- Informar periódicamente a los operarios de los resultados obtenidos, haciendo hincapié en los avances obtenidos por cada operario, implicando a toda la organización en la mejora continua y en el aumento de la producción / disponibilidad.
¿Qué beneficios aporta ?
- Crea un entorno de colaboración entre los equipos de mantenimiento y producción.
- Reduce el mantenimiento correctivo, ya que permite detectar fallos antes de que se produzcan las averías.
- Reduce la carga de trabajo del departamento de mantenimiento, que puede centrarse en tareas complejas que impliquen conocimientos técnicos avanzados, desmontaje de máquinas, calibraciones, etc.
- Permite minimizar la externalización de mantenimiento, reduciéndola únicamente a aquellos trabajos que tenga que realizar el fabricante para mantener garantías, etc.
- Aumenta la disponibilidad de máquina y reduce las averías. Nadie conoce la máquina mejor que el que quién la utiliza. El operario sabe cuál es el comportamiento normal y cuando las cosas comienzan a no ir bien.
- Implicación de todo el personal en el mantenimiento, que permite un mayor conocimiento de la instalación, facilita su operación y agiliza la toma de decisiones.
- Permite planificar mejor las paradas, realizándolas cuando no afecten a la producción y se cumplan con los criterios de seguridad necesarios.
- Los operarios están mejor capacitados, lo que les permite promocionar internamente.
- Como parte del TPM (Total Productive Maintenance)o MPT es un proceso de mejora continua, tanto de personas como de empresas.
Mantenimiento autónomo en siete pasos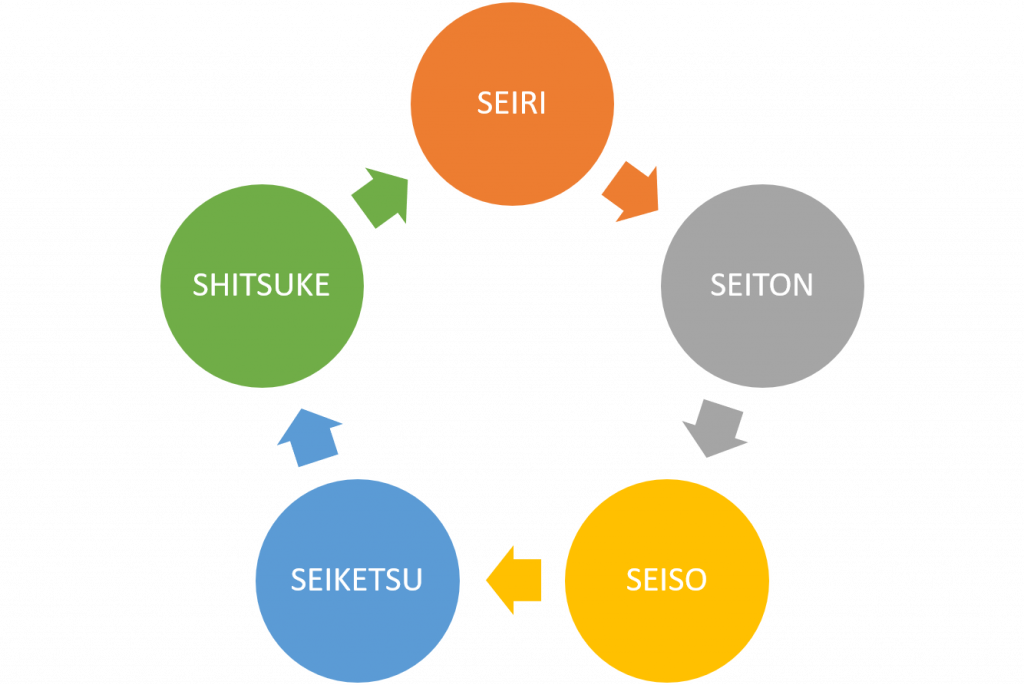
El TPM es considerada una metodología de Manufactura limpia (Lean Manufacturing), y se basa en las 5 S desarrollada por Toyota:
- Seiri: subordinar, clasificar, descartar
- Seiton: sistematizar, ordenar
- Seiso: sanear y limpiar
- Seiketsu: simplificar, estandarizar y volver coherente
- Shitsuke: sostener el proceso, disciplinar
Estos principios deben imperar en cada uno de los pasos de implementación del mantenimiento autónomo que suele tomar de tres a cinco años.
Tres primeros pasos para la prevención, detección y control de las condiciones fundamentales de los equipos (Seiri, Seiton, Seiso)
Limpieza
Hay que desarrollar el interés de los operadores y operarios por mantener limpias sus máquinas y por trabajar de una manera limpia y ordenada.
La limpieza es un proceso educativo; a veces se cree que el trabajo de limpieza no nos corresponde, más aún si existen personas que realizan este trabajo. Por ello, hay que preguntarse: ¿Por qué limpiar si el polvo o la grasa se acumula rápidamente? Una manera de comprender esta necesidad es la respuesta a esa pregunta: No existe vibración cuando un perno esta apropiadamente asegurado.
Proponer medidas para mantener la limpieza de los equipos
Cuando el operario desea mantener el equipo limpio, debe proponer medidas para combatir las causas que generan el desorden, la suciedad o los desajustes.
Estándares de limpieza y lubricación
Los determinan los grupos de trabajo del TPM. Son estándares que se aplican con el objetivo de un rápido y eficaz mantenimiento rápido, con el objetivo de prevenir el deterioro. Suelen incluir limpieza, lubricación y reapriete del equipo.
Cuarto y quinto paso para la detección y evaluación de los modos de fallo de un equipo (Seiketsu)
Inspección general del equipo.
Con anterioridad, el personal debe estar capacitado técnicamente para realizar la inspección general del equipo. De esta forma todo el personal tendrá habilidades y destrezas para detectar anormalidades.
Inspección autónoma.
Una vez realizada la inspección general, se compara y evalúa para eliminar cualquier inconsistencia. En este paso se hace un manual de inspección autónoma: se hacen programas de mantenimiento preventivo, de mantenimiento anual, listas de verificación y ajustes necesarios y un manual en caso de mantenimiento correctivo.
Pasos finales para sostener y mejorar (Shitsuke)
Organización y ordenamiento.
Organización y ordenamiento son las actividades de mejoramiento para fomentar, simplificar y organizar el mantenimiento autónomo, y la adhesión a los estándares y procedimientos En el paso 6, los líderes, mandos intermedios y directores toman el papel principal en complementar la implantación del mantenimiento autónomo por evaluación del papel de los operarios y clarificar sus responsabilidades.
Finalización de la implantación del mantenimiento autónomo.
Habiendo realizado los seis pasos anteriores, los profesionales serán más independientes y especializados. La formación y mejora de los pasos anteriores tendrá que realizarse mediante una auditoría continua, realizada por todos los niveles de personal indicados.
Conclusión
La utilización del mantenimiento autónomo en una empresa exige una importante inversión en formación, que garantice que todos los trabajadores conozcan como funciona la instalación y la función que realiza cada sistema dentro de la misma.
No obstante, esta inversión permitirá que los operarios realicen labores de mantenimiento sencillas que, a la larga, reducirán los costes y aumentarán la eficiencia, la disponibilidad y la productividad del centro.
Así mismo, La mejor preparación de los operarios permitirá detectar malfuncionamientos en las máquinas antes que se conviertan en averías, reduciendo el número y el coste de los correctivos.
¿Necesitas más información?- Contáctanos