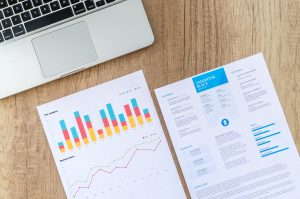
En este post daremos pistas sobre como Optimizar el Mantenimiento durante la Implementación de un GMAO. La instalación de un sistema de gestión de mantenimiento, no garantiza por si sólo la mejora en los procesos.
Para garantizar que esto sea así, es necesario realizar un estudio previo que garantice el éxito del proyecto.
Los tres objetivos principales de este estudio son: la reducción de órdenes de trabajo a realizar, evaluar si la empresa dispone de los medios necesarios (personal, materiales y herramientas) para realizar la carga de trabajo resultante y la creación de KPIs que nos sirvan como verificación y mejora de nuestra gestión.
Optimizar el mantenimiento reduciendo órdenes de trabajo:
- Organizar la documentación existente. Recopilar todos los planes de mantenimiento de las distintas máquinas. Es importante saber si tenemos información de mantenimiento de todos los equipos. Si no es así, es necesario pedírsela al fabricante o suministrador.
- Adecuar los planes de mantenimiento a las normativas y priorizar su realización.
- Analizar si se puede crear un trabajo que incluya otros. Por ejemplo, la revisión de las 5000 horas, puede incluir una serie de mantenimientos preventivos más pequeños.
- Agrupar los mantenimientos de equipos idénticos o similares en rutas de trabajo. Nos permite eliminar órdenes de trabajo, generando una única OT por ruta.
- Estudiar las órdenes de trabajo a realizar según el estado en el que se encuentre la máquina. Si creamos distintos estados de máquina (en funcionamiento, máquina parada, maquina averiada, etc..) y asignamos nuestros planes de mantenimiento a los estados de máquina en los que queremos que se realicen, reduciremos el volumen de OTs que el GMAO emitirá.
- Comprobar que gamas de mantenimiento es mejor lanzar manualmente. Hay trabajos de mantenimiento que únicamente se realizan bajo una serie de condiciones, que difícilmente pueden definirse utilizando frecuencias. Para este tipo de mantenimiento es mejor definir disparos manuales que el usuario pueda activar cuando sea necesario.
- Eliminar mantenimiento no rentable. Hay máquinas cuyo coste permite que se elimine todo su mantenimiento, a excepción de las pequeñas tareas de mantenimiento, y se substituya por otra unidad cuando se estropee.
- Revisar la frecuencia del mantenimiento contrastándola con la experiencia del personal de mantenimiento. Las frecuencias de mantenimiento del fabricante son un buen punto de partida. No obstante, cada máquina es diferente y es el personal de mantenimiento el que puede acortar o alargar la frecuencia de cada plan de mantenimiento basándose en su experiencia. Este punto es muy importante, nadie conoce mejor las máquinas que el personal que las mantiene.
La evaluación de la carga de trabajo asumible por nuestra plantilla de mantenimiento
Tiene que tener en cuenta el volumen de correctivo que tiene el centro, restando las horas del total de horas disponibles para la realización del mantenimiento preventivo.
Este análisis considerar la formación de los operarios, priorizando las tareas que sean más sencillas de realizar, teniendo en cuenta la capacitación de la plantilla.
También hay que valorar la externalización de tareas, en el caso que el coste de realización interna sea igual o superior o que las tareas necesiten de conocimiento o herramientas que solo tenga el fabricante /suministrador.
En el caso que no se quieran externalizar tareas, es necesario calcular el aumento de plantilla necesario para la realización interna de todo el trabajo resultante del estudio.
Definición de KPIs
Los KPIs son el corazón de la mejora continua en el mantenimiento y deben de ser definidos al comienzo del proyecto y optimizados continuamente.
Si hacemos un buen estudio previo de la situación de nuestro mantenimiento, podremos exprimir el 100% nuestro nuevo GMAO.
Juan Antonio Mojón
Director División Software